Nortek Variable Refrigerant Flow Systems (VRF or VRV) (8)
Browse Variable Refrigerant Flow Systems (VRF or VRV)
- Make
- Nortek
Variable Refrigerant Flow System (VRF or VRV) products updated recently
Variable Refrigerant Flow Systems (VRF or VRV) - Expert Commentary

The HVAC market is forecasted to grow at a projected compound annual growth rate (CAGR) of 3.9%, with a prediction to reach $370 billion by 2030. But in reality, the HVAC and plumb...

The demands of HVAC professionals are unique, often requiring them to work in extreme conditions that necessitate gear that can keep up. Every day, these workers face fluctuating t...
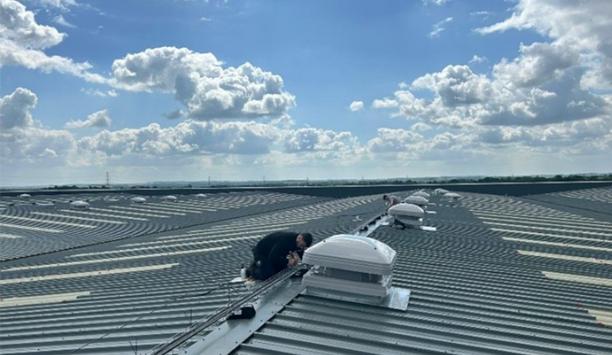
How can UK businesses effectively tackle the challenge of cooling commercial and industrial buildings? Cooling commercial and industrial buildings can be a challenge for UK busines...
Latest Nortek Global HVAC news
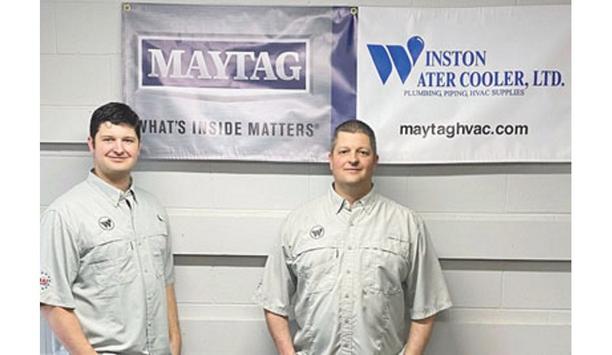
Nortek Global HVAC (NGH), a manufacturer of HVAC equipment, has named Winston Water Cooler, Lubbock, Texas, and Winsupply of Rio Grande Valley, Mission, Texas, as HVAC wholesale di...

Nortek Global HVAC (NGH), manufacturer of the unit heaters, has redesigned its entire Reznor® brand of commercial/industrial/residential gas-fired unit heaters for the North Am...

Madison Industries, one of the world’s largest privately held companies, announced an agreement to acquire Nortek Air, a pioneer in providing critical air management, thermal...