Air Filtration Systems (92)
Browse Air Filtration Systems
Air Filtration products updated recently
Air Filtration - Expert Commentary
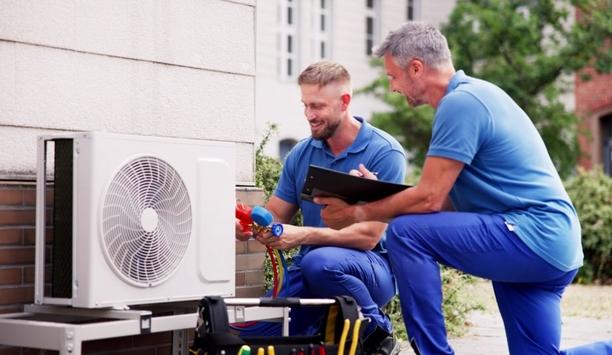
It’s an exciting and challenging time to be an HVACR professional. The industry is rapidly evolving to implement advanced technology and adapt to environmentally conscious re...

Hydrofluoroolefin (HFO) and so-called “natural” refrigerants have coexisted for more than two decades, with each serving the specific needs of the HVACR industry. How...
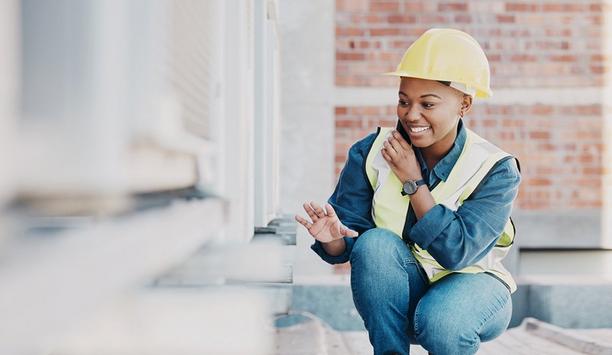
College was never the only path to success. There are many other nontraditional avenues to success, and I had the privilege of blindly venturing down one myself. My path included...