Daikin Energy Recovery Ventilators (ERV) (1)
Browse Energy Recovery Ventilators (ERV)
- Make
- Daikin
Energy Recovery Ventilator (ERV) products updated recently
Energy Recovery Ventilators (ERV) - Expert Commentary
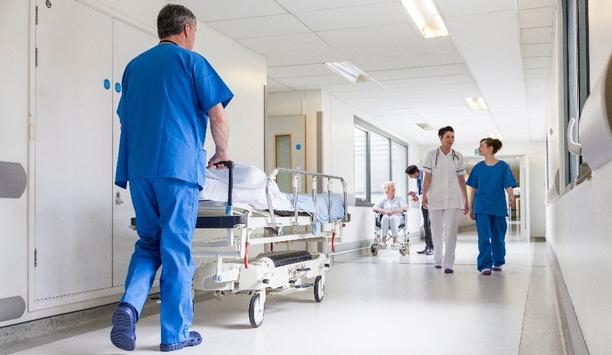
Advanced heating, ventilation, air-conditioning, and refrigeration (HVACR) systems have always been essential to healthcare. However, the need for clean, fresh air at the right tem...
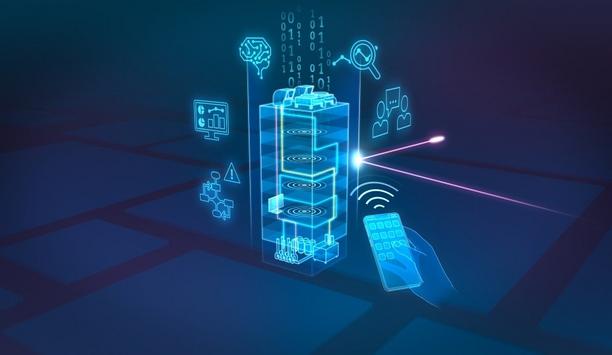
The importance of caring for the environment has become a top priority both around the world and increasingly in the United States. As regulations and social expectations become mo...
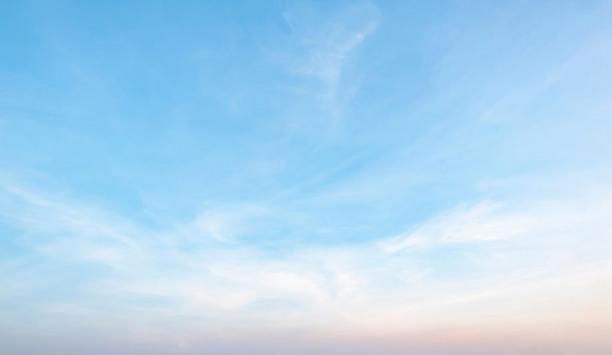
As COVID-19 becomes endemic and hybrid working becomes the norm, a great deal of time and energy is going into managing a safe return to the office and a move to new styles of work...
Latest Daikin Industries, Ltd. news
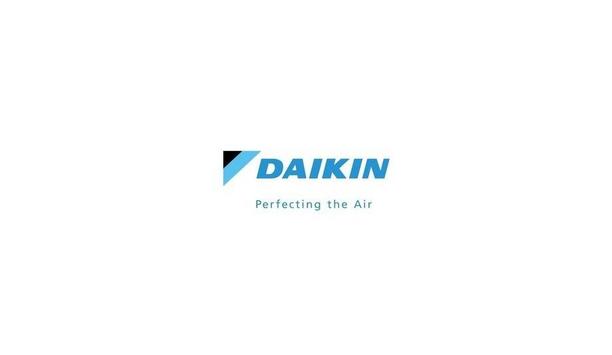
According to the British voting public, UK political parties aren’t doing enough to prioritize Sustainability in the upcoming election. With nearly two-thirds (64 percent)...

Buckinghamshire College Group and globally renowned heat pump provider, Daikin, in partnership with Quantum Group, have launched a new training facility for heat pump engineers, in...

Smart home expert - Hive and heat pump manufacturer - Daikin have announced the first step in a long-term collaboration to make net zero easier by helping customers control their h...