Daikin Geothermal units (3)
Browse Geothermal units
Geothermal products updated recently
Geothermal - Expert Commentary
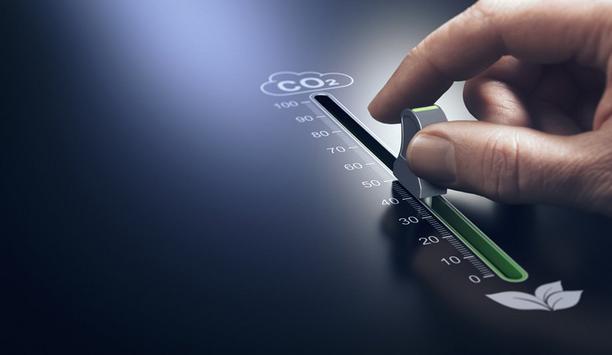
Peter Van Den Heede, Head of Sales and Marketing, Benelux, ABB Motion, explains how electrification systems are paving the way for sustainable urban landscapes. As the fight...
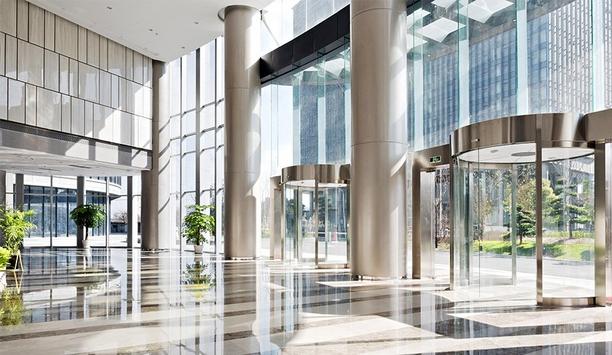
The past six months have been busy for those in HVAC as offices are updated and made safe for people to return. In addition to the various standard checks that need to be carried o...
Latest Daikin Industries, Ltd. news
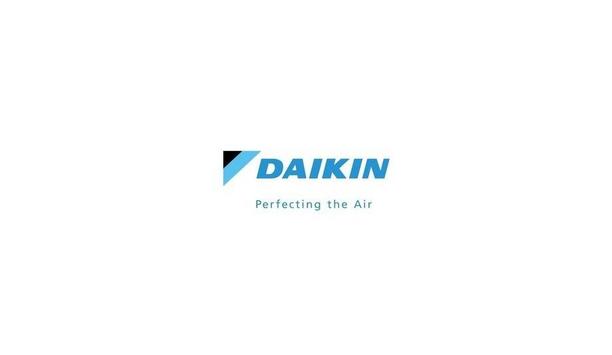
According to the British voting public, UK political parties aren’t doing enough to prioritize Sustainability in the upcoming election. With nearly two-thirds (64 percent)...

Buckinghamshire College Group and globally renowned heat pump provider, Daikin, in partnership with Quantum Group, have launched a new training facility for heat pump engineers, in...

Smart home expert - Hive and heat pump manufacturer - Daikin have announced the first step in a long-term collaboration to make net zero easier by helping customers control their h...