Goodman Heat Pumps (33)
Browse Heat Pumps
Heat Pump products updated recently
Heat Pumps - Expert Commentary

The demands of HVAC professionals are unique, often requiring them to work in extreme conditions that necessitate gear that can keep up. Every day, these workers face fluctuating t...
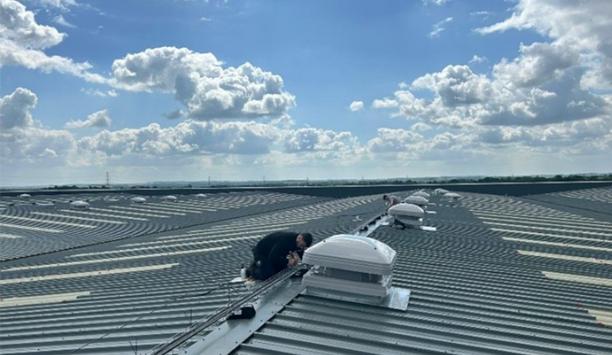
How can UK businesses effectively tackle the challenge of cooling commercial and industrial buildings? Cooling commercial and industrial buildings can be a challenge for UK busines...
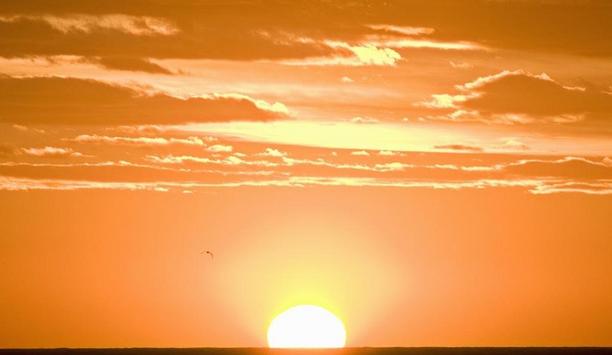
From temperate climates that reach mid-90 F in June and mild winters allowing people to be outdoors without jackets to the “May flowers” that bloom in early March, it&r...
Latest Goodman Manufacturing Company, L.P. news
TZOA pioneers of smart air quality technology for HVAC professionals and their homeowner customers, becomes HAVEN and announces the launch of the HAVEN central air controller. Alon...
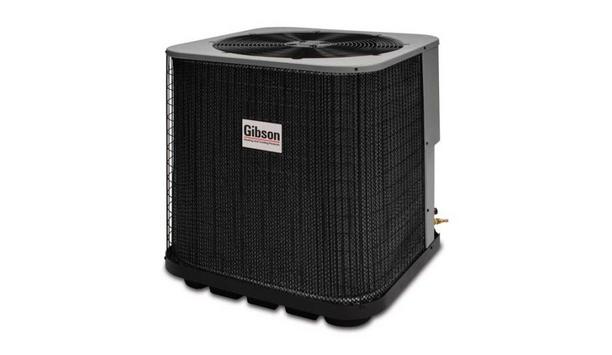
Manufacturers continue to make improvements in heat-pump technology, including higher efficiencies, contractor-friendly designs, and innovative extras like two-stage compressors th...
The Built In America television show is taking viewers deep inside one of the nation’s massive, new industrial facilities to witness how a $417 million investment in United S...