Goodman Air Handling Units (102)
Browse Air Handling Units
Air Handling Units products updated recently
Air Handling Units - Expert Commentary
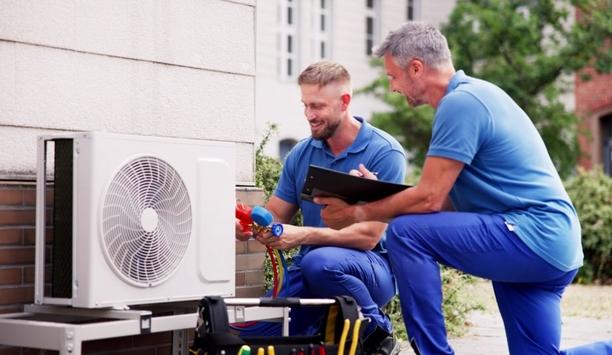
It’s an exciting and challenging time to be an HVACR professional. The industry is rapidly evolving to implement advanced technology and adapt to environmentally conscious re...

Hydrofluoroolefin (HFO) and so-called “natural” refrigerants have coexisted for more than two decades, with each serving the specific needs of the HVACR industry. How...
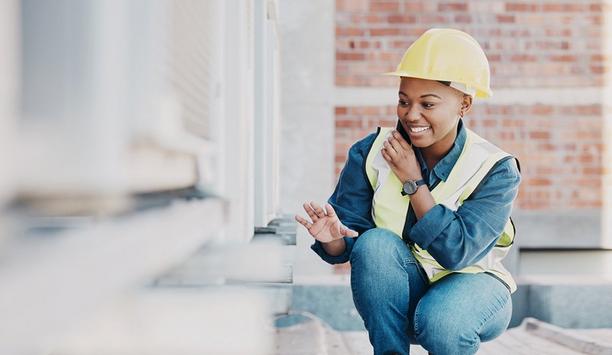
College was never the only path to success. There are many other nontraditional avenues to success, and I had the privilege of blindly venturing down one myself. My path included...
Latest Goodman Manufacturing Company, L.P. news
TZOA pioneers of smart air quality technology for HVAC professionals and their homeowner customers, becomes HAVEN and announces the launch of the HAVEN central air controller. Alon...
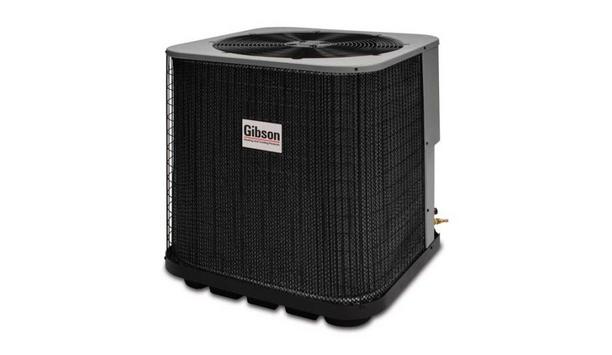
Manufacturers continue to make improvements in heat-pump technology, including higher efficiencies, contractor-friendly designs, and innovative extras like two-stage compressors th...
The Built In America television show is taking viewers deep inside one of the nation’s massive, new industrial facilities to witness how a $417 million investment in United S...