Johnson Controls Packaged Roof Top Units (RTUs) (21)
Browse Packaged Roof Top Units (RTUs)
- Make
- Johnson Controls
- Other Johnson Controls products
- Johnson Controls Economizers
- Johnson Controls Air Handling Units
- Johnson Controls Thermostats
- Johnson Controls Single Packaged Vertical Units
Packaged Unit/RTU products updated recently
Packaged Units/RTU - Expert Commentary
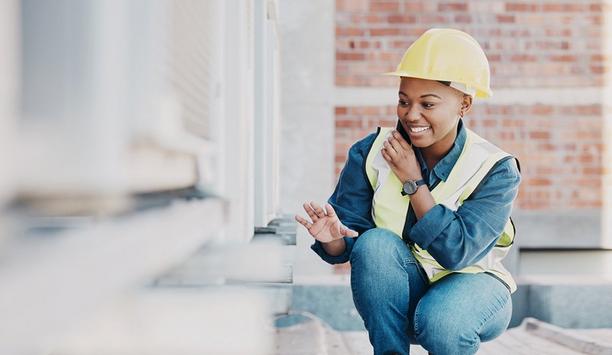
College was never the only path to success. There are many other nontraditional avenues to success, and I had the privilege of blindly venturing down one myself. My path included...
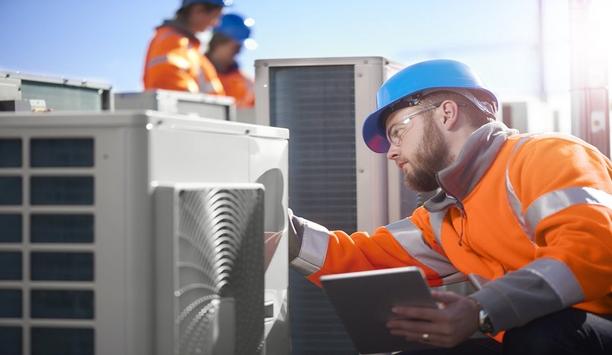
This time of year, a lot of planning is underway. Companies throughout the HVACR industry are mapping out the best path to maintain their current level of business, pursue growth w...
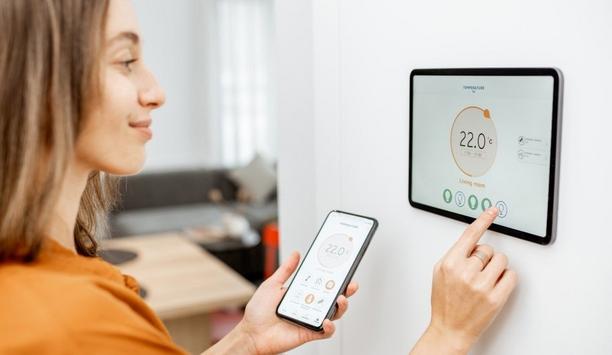
Using air conditioners and electric fans to stay cool accounts for nearly 20% of the total electricity used in buildings around the world, according to a report from the Internatio...
Latest Johnson Controls news
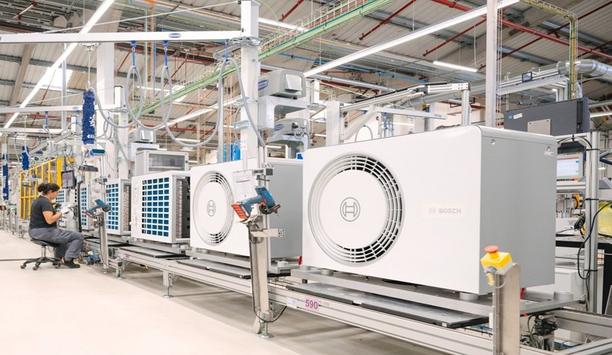
Bosch, the supplier of technology and services, is continuing its growth course with a strategic acquisition. For its Energy and Building Technology business sector, the Bosch Grou...

As the Paris Olympics 2024 is about to get underway, millions of fans will travel to the French capital city to attend one of the world's largest sporting events. Due to the...
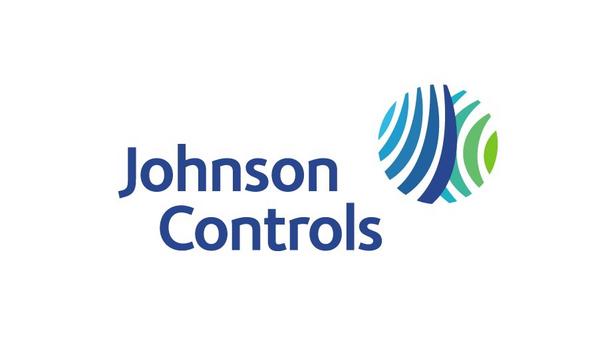
Johnson Controls, the global pioneer for smart, healthy, and sustainable buildings introduced the Sabroe UniSAB 4, an innovative industrial refrigeration system controller that exp...