Johnson Controls Thermostats (24)
Browse Thermostats
- Make
- Johnson Controls
- Other Johnson Controls products
- Johnson Controls Economizers
- Johnson Controls Air Handling Units
- Johnson Controls Single Packaged Vertical Units
Thermostats products updated recently
Thermostats - Expert Commentary
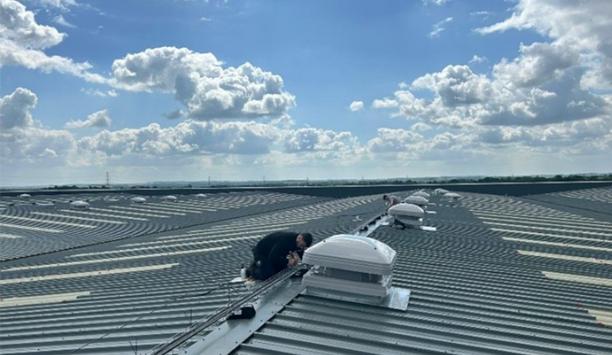
How can UK businesses effectively tackle the challenge of cooling commercial and industrial buildings? Cooling commercial and industrial buildings can be a challenge for UK busines...
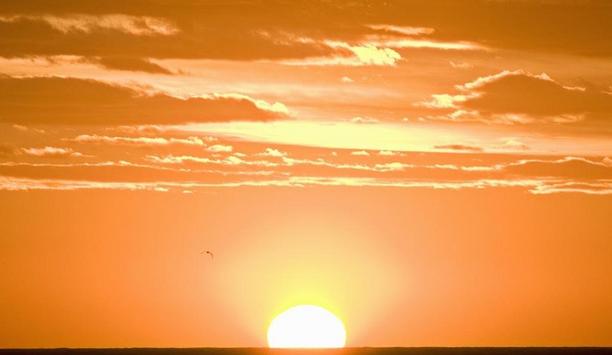
From temperate climates that reach mid-90 F in June and mild winters allowing people to be outdoors without jackets to the “May flowers” that bloom in early March, it&r...
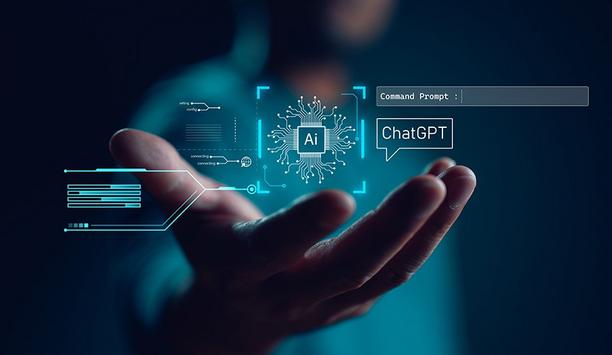
I remember Dr. Dave Bowman from Kubrick's "2001: A Space Odyssey" commanding HAL 9000 to open the pod bay doors, and HAL chillingly responds, "I'm sorry, Dave. I'm afraid I can't...
Latest Johnson Controls news
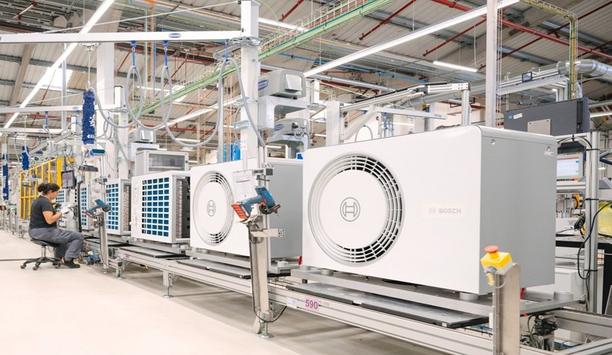
Bosch, the supplier of technology and services, is continuing its growth course with a strategic acquisition. For its Energy and Building Technology business sector, the Bosch Grou...

As the Paris Olympics 2024 is about to get underway, millions of fans will travel to the French capital city to attend one of the world's largest sporting events. Due to the...
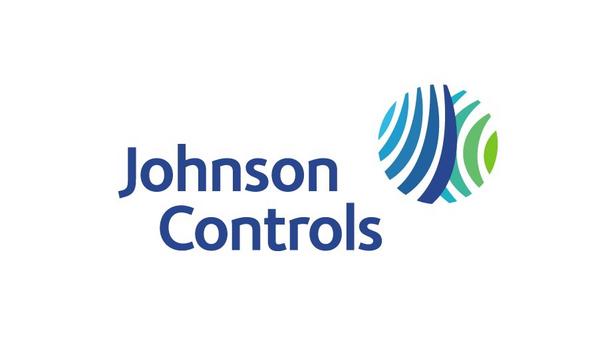
Johnson Controls, the global pioneer for smart, healthy, and sustainable buildings introduced the Sabroe UniSAB 4, an innovative industrial refrigeration system controller that exp...