Tempstar Evaporator Coils (14)
Browse Evaporator Coils
- Make
- Tempstar
- Other Tempstar products
- Tempstar Gas Furnaces
- Tempstar Oil Furnaces
- Tempstar Geothermal
- Tempstar Thermostats
- Tempstar Heat Pumps
Evaporator Coil products updated recently
Evaporator Coils - Expert Commentary
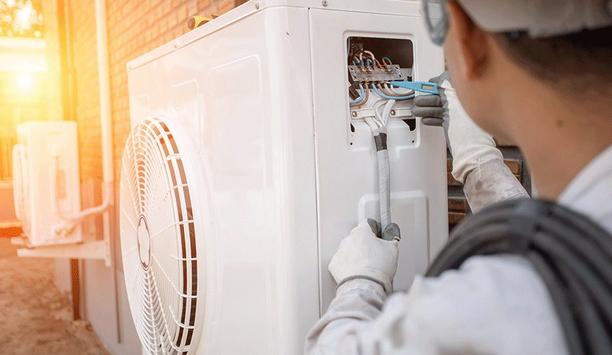
Seasonal transitions are the perfect time to take inventory and inspect a building’s various systems. We’ve been reminded for years that when we set our clocks back, we...

A cooling tower allows building owners and operators to take advantage of low cooling water temperatures and higher rates of heat rejection per square meter inherent in evaporative...
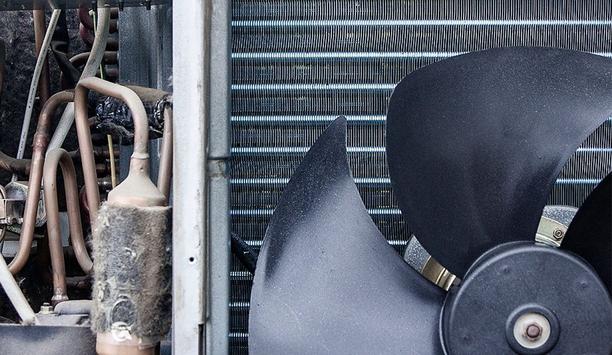
In what can only be described as a very turbulent year, many businesses have had to shut their doors and have all but forgotten about the general upkeep of their sites. With priori...