Tempstar Gas Furnaces (21)
Browse Gas Furnaces
- Make
- Tempstar
- Other Tempstar products
- Tempstar Oil Furnaces
- Tempstar Geothermal
- Tempstar Thermostats
- Tempstar Heat Pumps
Gas Furnace products updated recently
Gas Furnaces - Expert Commentary
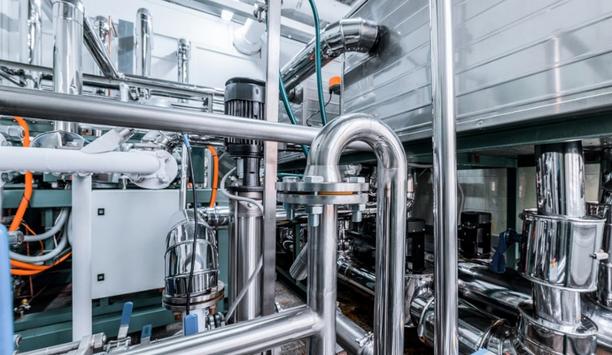
Although the European Union is several steps ahead in the transition away from hydrofluorocarbon (HFC) refrigerants, members of the HVACR industry in other countries currently find...
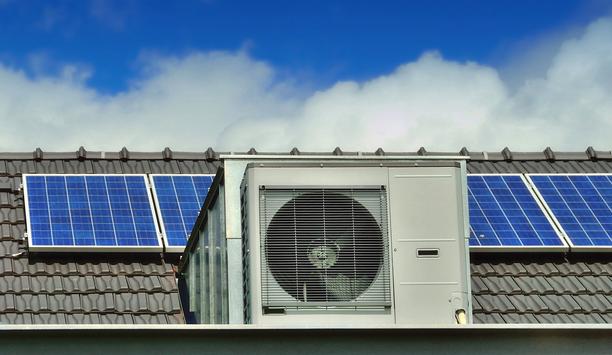
Every six years, the United States Department of Energy (DOE) reviews how much energy certain home appliances and mechanical systems use and determines if an increase in energy eff...
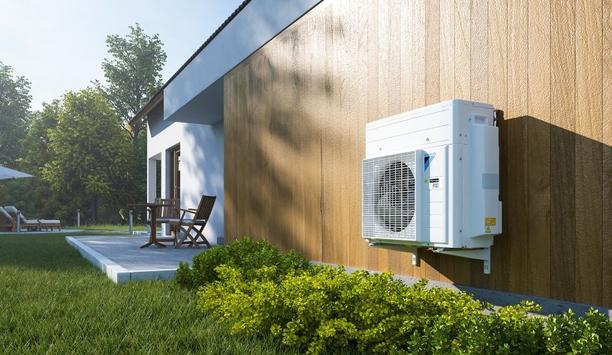
With the UK committed to reducing greenhouse gas emissions to zero by 2050, drastic action is needed by the government. For new-build homes, there’s a gas boiler ban coming...