Coleman Air Handling Units (71)
Browse Air Handling Units
Air Handling Units products updated recently
Air Handling Units - Expert Commentary
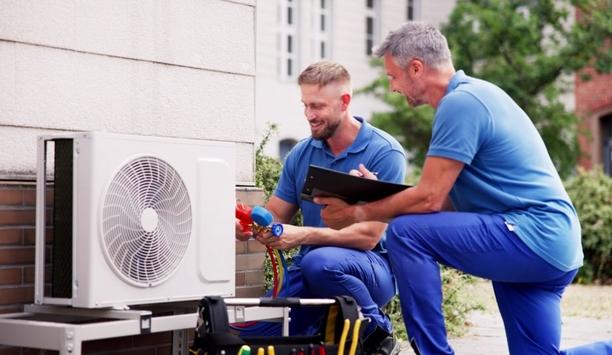
It’s an exciting and challenging time to be an HVACR professional. The industry is rapidly evolving to implement advanced technology and adapt to environmentally conscious re...

Hydrofluoroolefin (HFO) and so-called “natural” refrigerants have coexisted for more than two decades, with each serving the specific needs of the HVACR industry. How...
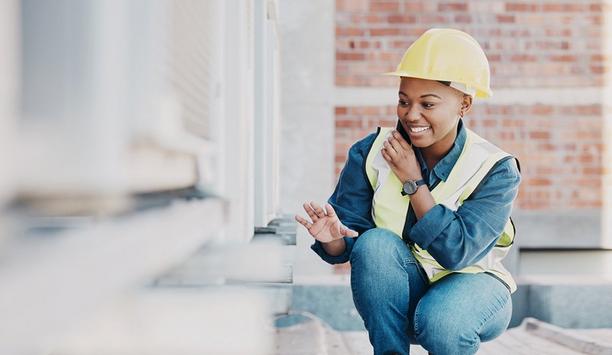
College was never the only path to success. There are many other nontraditional avenues to success, and I had the privilege of blindly venturing down one myself. My path included...
Latest Coleman (Johnson Controls) news
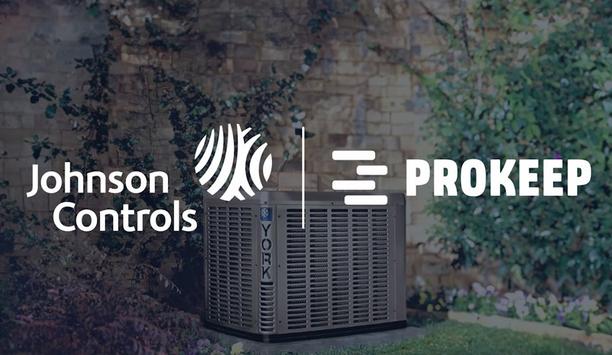
Prokeep, the distribution's pioneering communication engagement software, announced that it will work with Johnson Controls as a preferred vendor-offering its brand distributors' c...
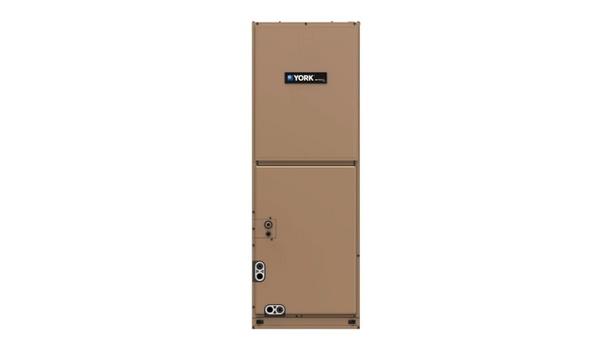
Johnson Controls, the pioneer for smart, healthy and sustainable buildings, announces the launch of a new, redesigned line of high-efficiency air handlers that will improve comfort...
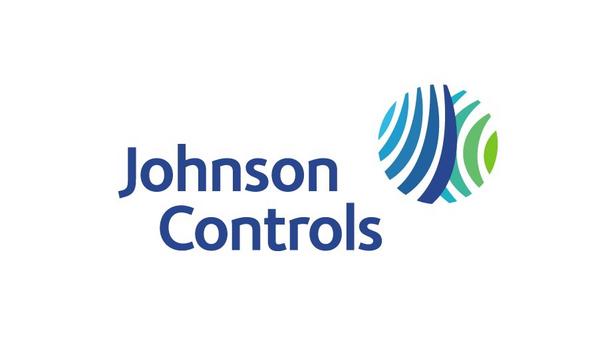
Johnson Controls, the pioneer for smart, healthy, and sustainable buildings, announces new emergency relief rebates that HVAC contractors can offer eligible homeowners who live in...