Haier Window Air Conditioners (A/Cs) (16)
Browse Window Air Conditioners (A/Cs)
- Make
- Haier
- Other Haier products
- Haier Mini-Split Systems
Window A/C products updated recently
Window A/C - Expert Commentary
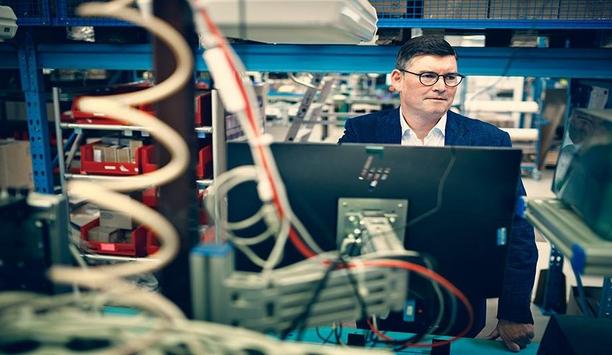
Energy bills for small businesses have become a major issue throughout 2023. As prices have risen drastically over the last twelve months, SMEs have been relying on the government&...
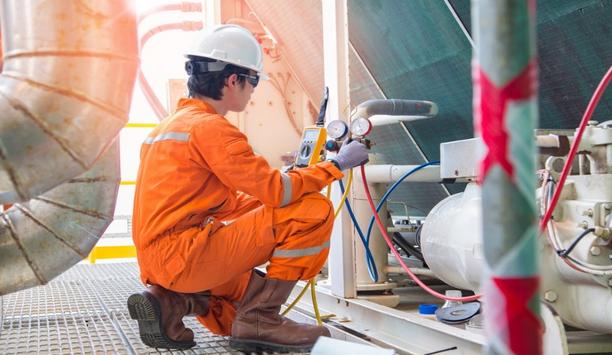
Each day we’re reading headlines about decarbonization ambitions for buildings while challenged with supporting day-to-day operational needs. Yet, we’re still tasked wi...
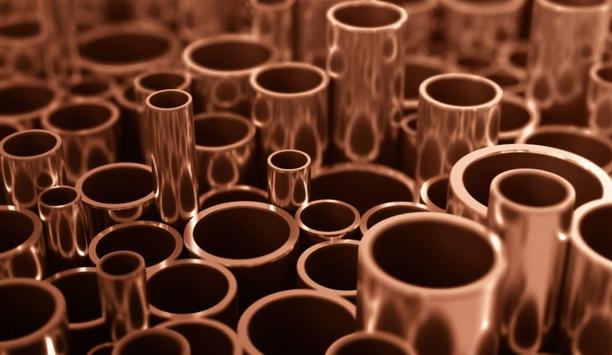
With the UK experiencing increasingly warmer summers and more frequent heatwaves, we’re equally seeing more air conditioning units installed in both commercial and residentia...
Latest Haier news

Deane Flint has joined Fujitsu General Air Conditioning UK as Chief Operating Officer. Ian Carroll moves to become Deputy Chief Executive Officer and retains overall responsibility...
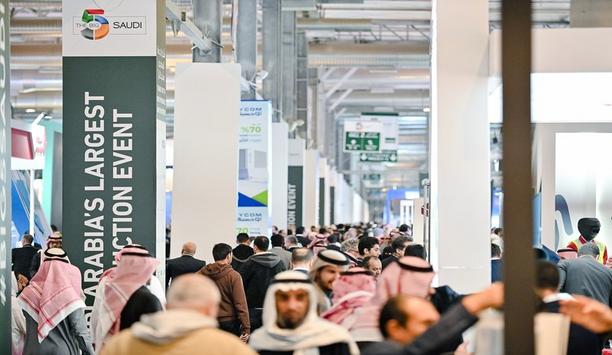
Saudi Arabia’s construction sector is expected to grow at an average annual rate of 4% between 2024 and 2027, driven by strategic initiatives focused on economic diversificat...

Carrier Global Corporation, a globally renowned company in intelligent climate and energy solutions, entered into a definitive agreement to sell its global commercial refrigeration...