Lennox Thermostats (12)
Browse Thermostats
Thermostats products updated recently
Thermostats - Expert Commentary
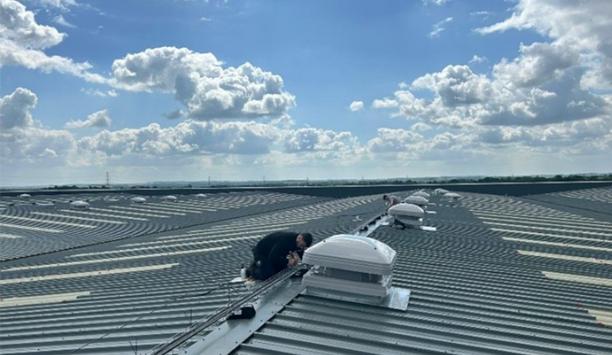
How can UK businesses effectively tackle the challenge of cooling commercial and industrial buildings? Cooling commercial and industrial buildings can be a challenge for UK busines...
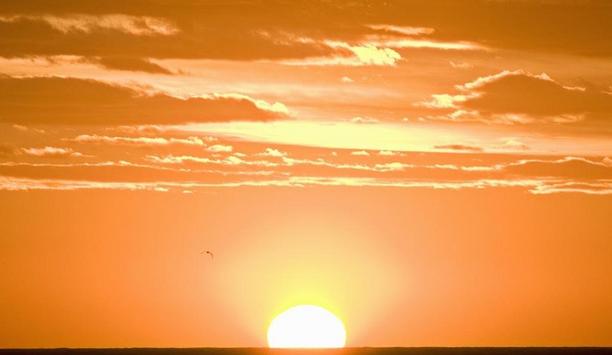
From temperate climates that reach mid-90 F in June and mild winters allowing people to be outdoors without jackets to the “May flowers” that bloom in early March, it&r...
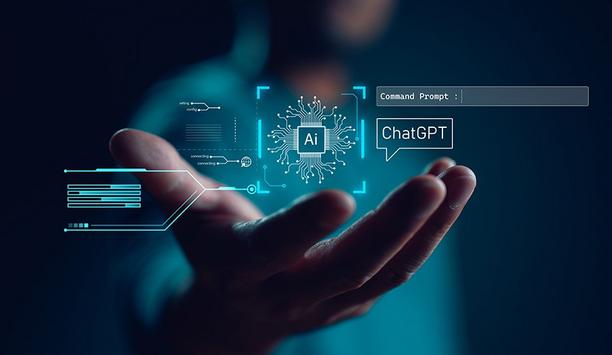
I remember Dr. Dave Bowman from Kubrick's "2001: A Space Odyssey" commanding HAL 9000 to open the pod bay doors, and HAL chillingly responds, "I'm sorry, Dave. I'm afraid I can't...
Latest Lennox news

Budderfly, the preferred sustainability partner for commercial businesses with repeatable footprints, is partnering with trade schools nationwide to address the persistent lack of...

Eurovent has welcomed one of the pioneering HVACR solution providers, LENNOX EMEA, as a new member. LENNOX EMEA’s membership significantly expands Eurovent’s base, supp...
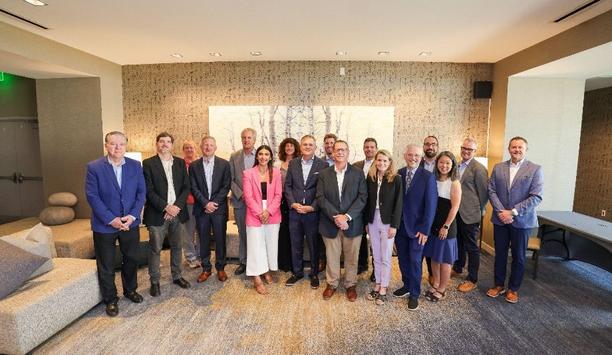
The California Heat Pump Partnership (CAHPP) officially launched its first convening to bring together state agencies, manufacturers representing more than 90% of the U.S. consumer...