YORK Gas Furnaces (68)
Browse Gas Furnaces
Gas Furnace products updated recently
Gas Furnaces - Expert Commentary
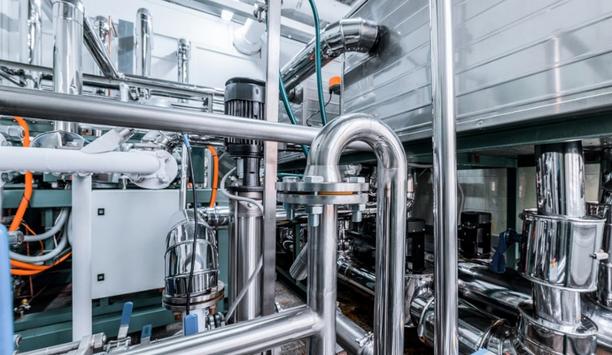
Although the European Union is several steps ahead in the transition away from hydrofluorocarbon (HFC) refrigerants, members of the HVACR industry in other countries currently find...
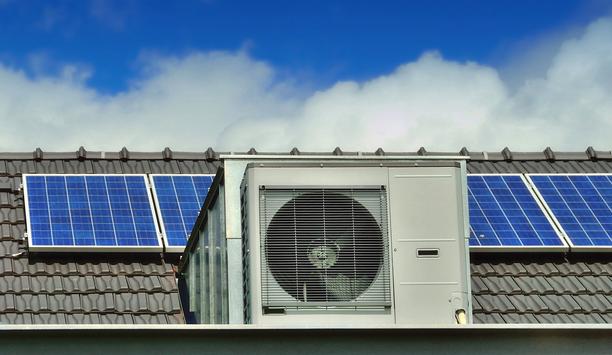
Every six years, the United States Department of Energy (DOE) reviews how much energy certain home appliances and mechanical systems use and determines if an increase in energy eff...
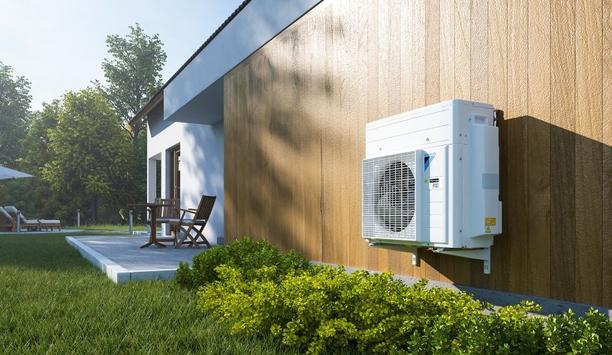
With the UK committed to reducing greenhouse gas emissions to zero by 2050, drastic action is needed by the government. For new-build homes, there’s a gas boiler ban coming...
Latest YORK Heating news
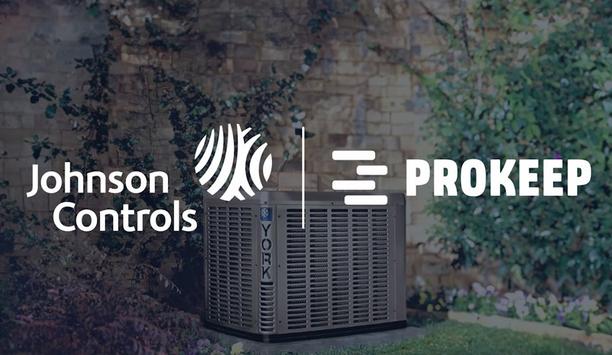
Prokeep, the distribution's pioneering communication engagement software, announced that it will work with Johnson Controls as a preferred vendor-offering its brand distributors' c...
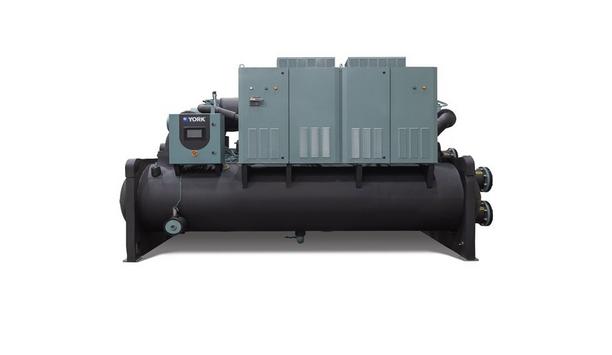
Johnson Controls, the globally renowned company for smart, healthy, and sustainable buildings, announced the launch of the YORK® YVWH Water-to-Water Dual Variable Speed Screw H...

Parts Town, the technology innovator and market-renowned distributor of original equipment manufacturer (OEM) food service parts, residential appliance parts, and related products,...