Bryant Thermostats (16)
Browse Thermostats
- Make
- Bryant
Thermostats products updated recently
Thermostats - Expert Commentary
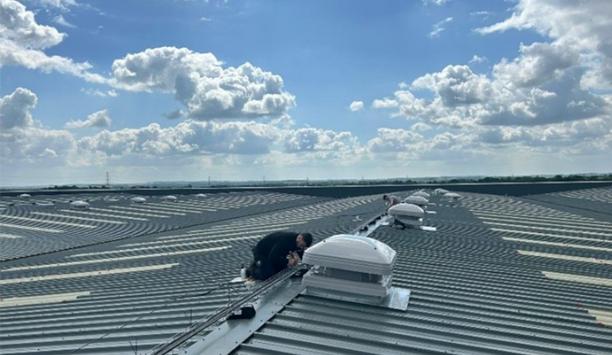
How can UK businesses effectively tackle the challenge of cooling commercial and industrial buildings? Cooling commercial and industrial buildings can be a challenge for UK busines...
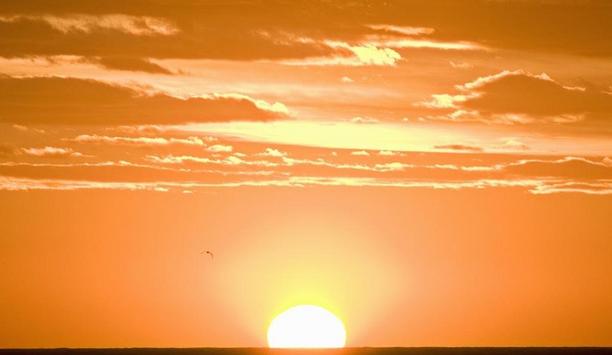
From temperate climates that reach mid-90 F in June and mild winters allowing people to be outdoors without jackets to the “May flowers” that bloom in early March, it&r...
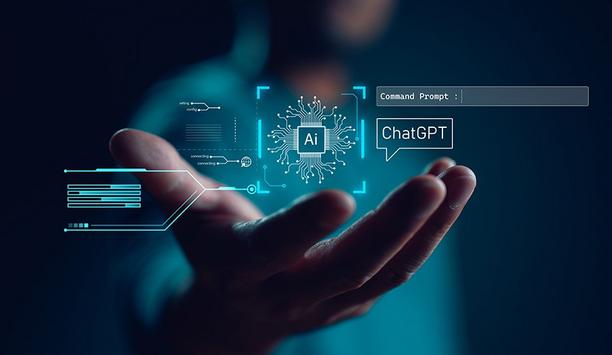
I remember Dr. Dave Bowman from Kubrick's "2001: A Space Odyssey" commanding HAL 9000 to open the pod bay doors, and HAL chillingly responds, "I'm sorry, Dave. I'm afraid I can't...
Latest Bryant Heating & Cooling Systems news
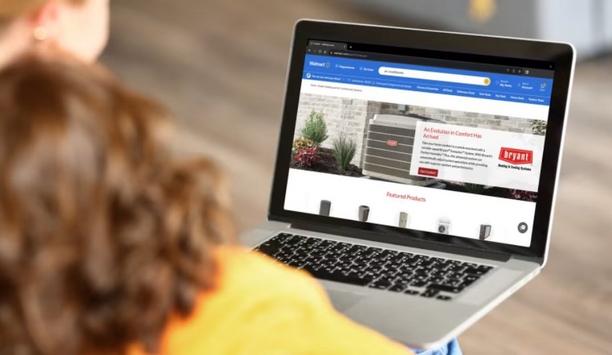
Walmart, the second largest eCommerce provider in the U.S., will begin directing HVAC inquiries to Bryant Heating & Cooling dealers as it expands its available offering to its...
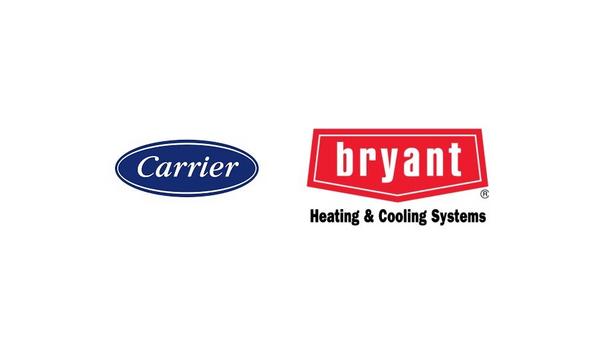
Carrier and Bryant have announced the recipients of this year’s Carrier & Bryant Distributors’ Education Foundation scholarships. Recipients will rec...
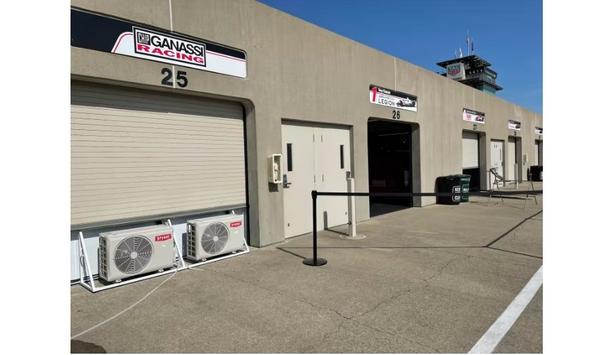
Bryant announced the installation of Bryant ductless systems in all Chip Ganassi Racing garages in support of cool, comfortable workstations. Bryant is once again sponsoring Tony K...